The world’s infrastructure is aged continuously, thousands of kilometres of pipelines need to be rehabilitated. The main reason for this problem is corrosion. Internally unprotected concrete sewer pipes are rapidly deteriorated by the presence of sulfuric acid in a sanitary sewer system. Externally, soil conditions and stray electrical currents can deteriorate underground pipes. Metallic pipes can corrode when placed in poorly aerated, poorly drained soils of low resistivity. Precautions by corrosion-resistant material systems and corrosion protection systems will be caused to higher pipelines costs. Corrosion is a non-reversible process. There is one simple way to fully eliminate this problem: GRP PIPE.
GRP pipes are long-lasting, corrosion-resistant, lightweight fibreglass-reinforced polyester (GRP) pipes. It is an ideal pipe material for drinking water and sewage networks for rainwater drainage systems and fire water networks and industrial solutions. It is made with a rounding cylinder process, the most modern technology in the production of GRP pipelines. This method can be used to make tubular fibres between 10 cm and 4 meters in diameter. The process uses glass fibre, polyester resin and quartz sand, in addition to which chemical additives are used for surface coating.
To enhance performance, GRP pipes are designed as a composite of fibre, resin, and filler in multiple layers. Pipes with different characteristics can be manufactured through the engineering design of the layers. Filament winding is the process of impregnating glass fibre reinforcement with resin, then applying the wetted fibres onto a mandrel in a prescribed pattern. Chopped glass rovings may be used as supplemental reinforcement. The quality of all raw materials should be approved prior to their use for GRP pipes. The production process is operated automatically by computer-controlled machines. This leads to a standard and consistent quality in GRP pipes.There are two types of GRP pipes: Uniaxial and Biaxial. Either type is flexible. Uniaxial pipes can only support hoop stress (radial and tangential) while biaxial pipes are capable of bearing both hoop and axial stresses. Uniaxial pipes are appropriate for burial purposes and biaxial pipes are mainly used for above-ground installations. Uniaxial and biaxial pipes can be made into GRP, GRV, GRVE, and GRE by changing the layers, type of resin etc. to adapt to various mechanical requirements or chemical environments.
- corrosion-resistant
- long service life
- low maintenance costs
- lightweight product
- easy to transport and install
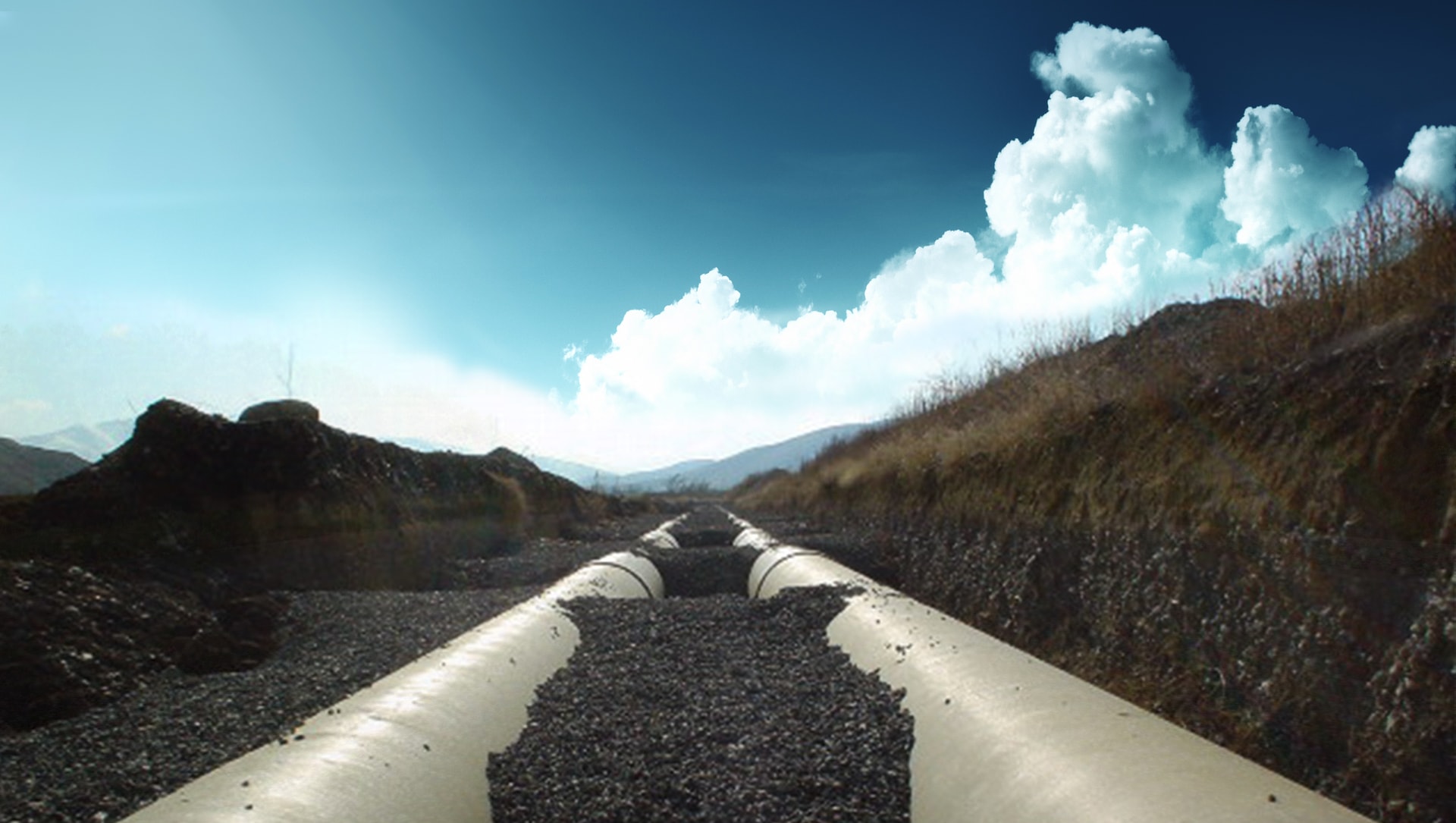
Fields of application
- as water transmission and distribution pipes
- for rainwater drainage systems
- for hydropower projects
- as a cooling water pipe
- in power plants for circulating water supply and blowing
- as a pipe material for irrigation and drainage systems
- for fire water networks
- for industrial applications
- as water reservoirs and tanks
- pumping systems
- for reconstruction projects
Advantages of the product
- fibreglass-reinforced polyester (GRP) pipes
- extremely strong
- high load capacity
- efficient operation
- low operating
- sustainable and affordable
- cost-effective solution
Key benefits
- corrosion-resistant
- long life
- low shipping and installation and maintenance costs
- lightweight (75% lighter in the same performance class as ductile iron pipes, 90% lighter in concrete pipes)
- long fibre sizes (can be produced up to 18 meters long, depending on the customer's needs)
- delivering more fluid relative to other types of pipes
- energy saving in a pumping system and less operating cost
- abrasion resistance
- available customary diameters and lengths
- project-specific pipe production at customer’s request
- straightforward installation
- advanced pipe design
Technical data
- Diameter: DN 100 - 4000 mm
- Pressure: PN 1 - 40 bar
- Stiffness: SN 1250 - 10000 Pa
- The process uses fiberglass and polyester resin and quartz sand in addition to which chemical additives are used for surface coating
- This method can be used to make tubular fibers between 10 cm and 4 meters in diameter.